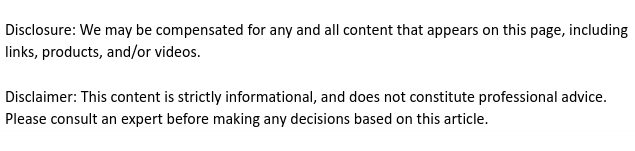

The robots are here and they’re hard at work. The Automatic Guided Vehicle systems used in warehouse and distribution centers for multiple functions are robots cutting down on hard labor and saving time and effort. More R2D2 than Attack of the Killer Robots, their goal is to help people lead better and more productive lives. Their use helps industrial manufacturing, warehouse and distribution centers to improve their operating efficiencies. They can be serviced and charged on the go, reducing time out. With a steady supply of agv parts, the productivity and cost efficiency receive a sizable boost.
The robots are here
And they’re a friendly, hardworking lot. Most of them, over 90%, actually work in factories. Half of all robots made today work in car manufacturing. Not only are the cars of the future high tech vehicles in themselves, they’re being made by an automated work force. The real jump in the use of industrial robots has occurred between 1993 and 2007, with the GDP contribution of automated manufacturing increasing by 0.37% in this period.
By 2015, the robotics market was worth $71 billion. The demand for automated guided vehicle systems or AGV is rising worldwide, fueled by their increased use in manufacturing. By 2015, it was up to 16,000 units, representing an annual increase of 35%. The worldwide market for AGVs was valued at $838.3 million in 2015 and will rise sharply to $2.3 billion by the end of 2024.
AGV systems in the auto manufacturing industry
Automated guided vehicle systems or AGV are automated modern logistics equipment. Widely used in the manufacturing, warehousing and distribution industries, they perform a whole range of functions efficiently and easily. They are also used in the automobile and power industries.
In the automobile industry, they perform functions like automobile assembly, engine, and transmission assembly lines. As the automation of the automobile production line continues, demand for AGVs in automobile industry is projected to increase to 10,500 units by 2020.
AGV Systems in warehousing and retrieval
Automated storage and retrieval systems are used in warehousing and distribution facilities for a range of tasks these include order picking, storage, kitting, consolidation, assembly, production and replenishments. They are also used for security and in retail.
There are many benefits to using AGV systems. They increase accountability and tracking of materials and parts, balancing of production line operations and elimination of production backups, and cost control. Maintenance is simple, with charging stations and a regular supply of agv parts.
AGV parts and service
Given the rapid rise in the use of AGV systems, the demand for AGV parts and servicing is also increasing. AGV systems generally need to be recharged after every eight to twelve hour shift. Automatic opportunity battery charging stations can be installed throughout the path, making it unnecessary to remove the vehicle from service.
Sometimes, special parking areas can be set up as charging positions. Charging is quick, and a 2 minute charge provides 20 to 30 minutes of working capacity. A regular supply of AGV parts can keep an assembly line or warehousing operation functioning smoothly.
Unlike the automated dystopias imagined throughout the last century, AGV systems actually make manufacturing and other heavy tasks easier, more accurate and more cost efficient. AGV systems are giving us a chance to lead more productive and fulfilling lives.